General
Seamos honestos, todos sabemos que cuanto más simple, mejor. La simplicidad de una bomba dosificadora de estilo peristáltico la convierte en un método muy confiable para inyectar una amplia variedad de productos químicos en aplicaciones de tratamiento de agua. Comprender las variables que provocan el desgaste de los componentes de la bomba, especialmente el desgaste del conjunto del tubo de la bomba, puede ayudar al lector a especificar correctamente la bomba para una aplicación específica.
Tecnología de bomba peristáltica
El cuerpo humano utiliza la acción de "peristaltismo" para mover los alimentos a través del tracto digestivo. Las contracciones musculares en forma de ondas aprietan progresivamente el tracto digestivo, esencialmente "empujando" la comida. No hay nada más simple que eso.
Uno de los mayores beneficios de una bomba peristáltica es su simplicidad funcional. Las bombas peristálticas utilizan un "cabezal" de bomba circular y un rodillo giratorio simple que está diseñado para pellizcar la tubería y exprimir suavemente el fluido a través de una tubería especialmente diseñada, como se muestra en la Figura 1.
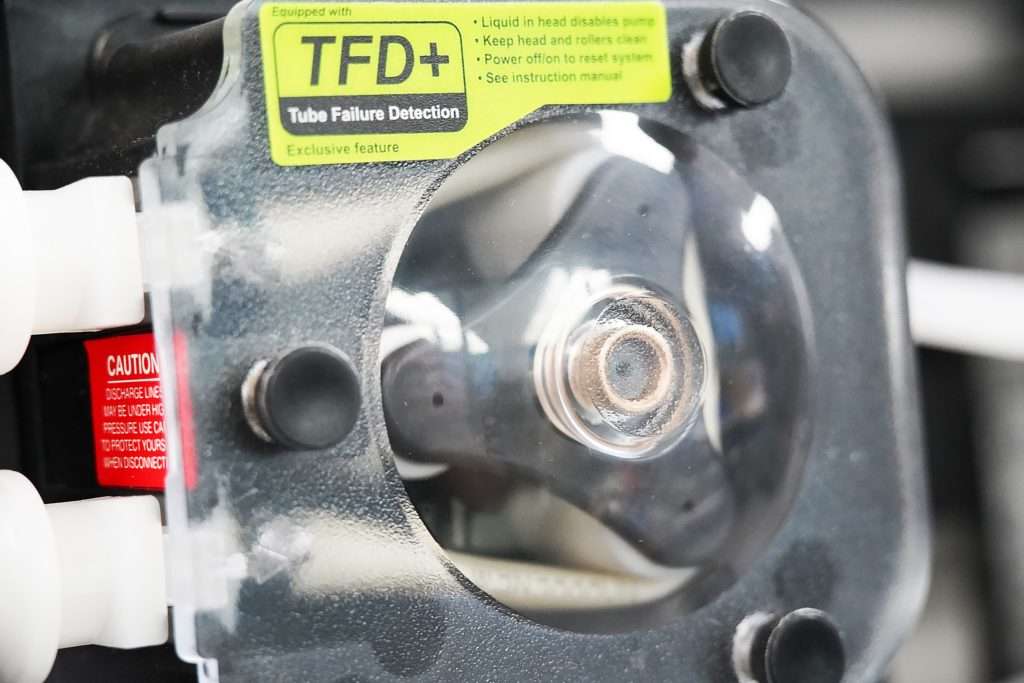
Pueden bombear fluidos y gases de manera efectiva, eliminando la posibilidad de sifonaje, bloqueo de vapor o pérdida de cebado incluso cuando operan a tasas de salida muy bajas. La salida casi continua da como resultado una dispersión más fina del producto químico en el sistema de tuberías en comparación con las bombas de tipo pulsante, como las bombas de diafragma. La figura 2 muestra la salida casi continua del producto químico en la corriente de flujo cuando se usa una bomba peristáltica frente a la dispersión química interrumpida cuando se usa una bomba de diafragma.
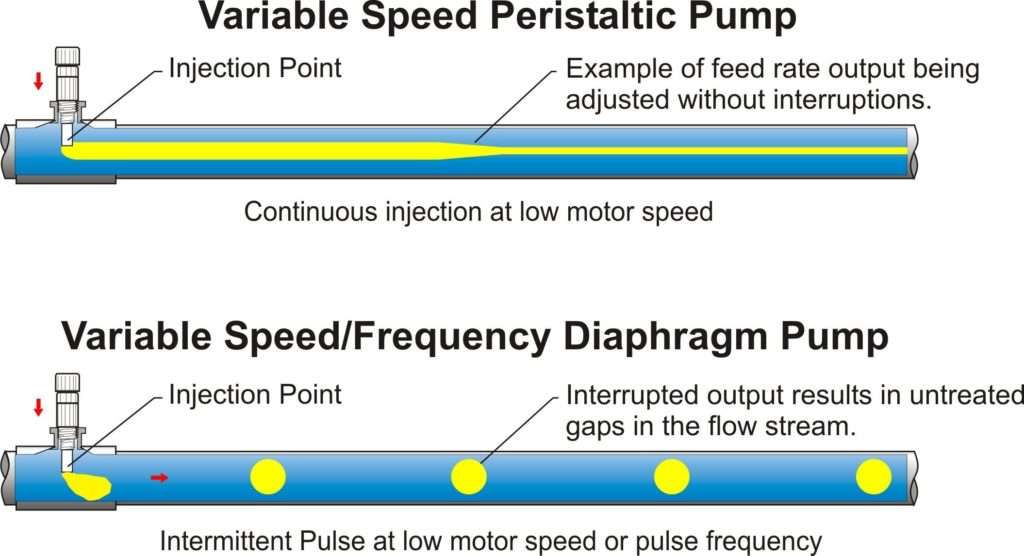
Menos componentes dan como resultado costos de mantenimiento muy bajos en comparación con el costo de reconstruir bombas más complejas que requieren una gran cantidad de componentes húmedos, como resortes metálicos, juntas tóricas, válvulas, bolas de retención, etc.
Comúnmente llamada bomba de tubo de presión, la nueva generación de bombas dosificadoras peristálticas de productos químicos es bastante diferente de las bombas de laboratorio de baja presión que la mayoría de las personas conocen en un entorno hospitalario. Estos caballos de batalla industriales ahora son capaces de bombear productos químicos agresivos como hipoclorito de sodio al 12 % (cloro), hidróxido de sodio al 50 %, ácido sulfúrico al 97 % y ácido fosfórico al 85 % contra presiones del sistema de hasta 125 psi. Algunos modelos incluyen características tales como sistemas de detección de fallas de tubos, sensores de verificación de flujo y electrónica de control sofisticada para interfaz PLC y conexión a sistemas SCADA.
Componentes del sistema de bombeo
A efectos de análisis, el conjunto de la bomba peristáltica se puede dividir en cinco componentes principales; 1. tubo de la bomba, 2. cabezal y rodillo de la bomba, 3. motor, 4. electrónica de control y 5. carcasa del motor/electrónica. Tenga en cuenta que en algunos modelos, los componentes electrónicos de control (VFD, arrancador de motor, PLC, etc.) están alojados en un gabinete separado.
Variables del desgaste de la tubería
Muchos fabricantes califican la vida útil de sus tuberías según el número de horas de funcionamiento efectivas antes de la falla. Si bien esta clasificación puede ser efectiva para comparar la vida útil de los tubos utilizados en la misma bomba bajo un conjunto específico de parámetros operativos (por ejemplo, bombear agua con un tipo de cabezal de bomba específico, a 0 psi, a RPM fijas), hay muchos variables que afectarán la cantidad de horas que un tubo dado durará en una aplicación real. Se debe tener cuidado al especificar los componentes de la bomba y los parámetros operativos para lograr la mayor vida útil posible del tubo en una aplicación.
- materiales de tubería – El material de la tubería debe resistir el químico que se inyecta, volver a su forma original después de muchos miles de oclusiones (compresiones) y operar a la presión requerida del sistema. Especificar el material de tubería óptimo es fundamental para una aplicación exitosa.
- Resistencia química – La incompatibilidad química dará como resultado una ruptura de las propiedades del material de la tubería, que a menudo se manifiesta como un cambio en la rigidez del material, ya sea ablandamiento o endurecimiento. En la mayoría de los casos, los problemas de resistencia química serán evidentes dentro de los primeros días de uso. Sin embargo, en algunos casos, el producto químico atacará el material de la tubería lentamente durante un largo período de tiempo, lo que reducirá la vida útil de la tubería.
- Dimensiones – Los diámetros de tubo más grandes y los espesores de pared más delgados generalmente darán como resultado una expectativa de vida útil reducida del tubo.
- Propiedades materiales – Las propiedades físicas del material del tubo influirán en gran medida no solo en su idoneidad para el uso general en una bomba peristáltica, sino también en la duración del tubo en una aplicación particular. El tubo de la bomba peristáltica debe ser capaz de volver con precisión a su forma original miles de veces después de ser apretado por el rodillo. Muchos materiales de tubería carecen de esta memoria, lo que los hace insatisfactorios para aplicaciones de bombas peristálticas. Los fabricantes de tubos ofrecen una variedad de formulaciones de tubos, muchas de las cuales son adecuadas para usar en bombas peristálticas y muchas otras no. El usuario final debe tener cuidado al seleccionar el material de la tubería para la aplicación. La mayoría de los proveedores de bombas ofrecerán asistencia con la selección de tubos u ofrecerán "ensamblajes de tubos" preensamblados diseñados específicamente para sus bombas peristálticas, lo que reduce en gran medida la posibilidad de una aplicación incorrecta.
- Presión del sistema – Las presiones que actúan sobre la tubería afectarán directamente la vida útil de la tubería. Se deben considerar las presiones de entrada y salida y se debe prestar especial atención a las variables "ocultas" que pueden aumentar la presión del sistema, como los componentes del sistema de tuberías y la viscosidad del fluido.
- Presión del sistema – La variable más obvia (y quizás la más influyente) que afecta la vida útil del tubo es la presión del sistema de tuberías. Pero a menudo, se pasan por alto los componentes del sistema y los factores de instalación que pueden aumentar la presión en el tubo de la bomba. Por ejemplo, la mayoría de los fabricantes recomiendan instalar una válvula de retención en la tubería de descarga directamente después del tubo de la bomba para evitar que el fluido del sistema fluya de regreso a través de la bomba durante el mantenimiento de rutina de la bomba o la ruptura del tubo de la bomba. Una válvula de retención cargada por resorte o una válvula de contrapresión aumentará la presión en el tubo de la bomba en un valor igual a la presión de apertura de la válvula. Por ejemplo, si la presión del sistema es de 50 psi y la válvula de contrapresión está ajustada a 20 psi, la presión efectiva en el tubo de la bomba es de 70 psi. Por lo tanto, deben evitarse las válvulas con altas presiones de apertura.
- Otra variable que a menudo se pasa por alto y que puede aumentar la presión en el tubo de la bomba es la distancia física desde la bomba hasta el punto donde se inyecta el producto químico en el sistema, lo cual es especialmente importante cuando se inyectan fluidos viscosos. La presión en el tubo de la bomba aumentará a medida que aumente la distancia desde el punto de inyección, aumente la viscosidad química y disminuya el diámetro de la tubería de descarga. ¡Imagine tratar de beber un batido espeso a través de una pajilla delgada de 100 pies! También se deben evitar los orificios de diámetro pequeño en los accesorios cuando se bombean productos químicos viscosos.
- Número de oclusiones – La vida útil del tubo se ve afectada por el número de veces que se debe pellizcar el tubo (número de oclusiones) para bombear una determinada cantidad de producto químico. La reducción del número de oclusiones aumentará la vida útil del tubo. Cuatro variables afectan el número de oclusiones necesarias para inyectar una determinada cantidad de líquido; el diámetro de la tubería, el diámetro del cabezal de la bomba, el número de rodillos en el conjunto de rodillos (oclusiones por revolución) y las rpm del motor. Algunos fabricantes utilizan el número total de oclusiones, en lugar del tiempo, al estimar la expectativa de vida útil del tubo.
- Diámetro de la tubería – Un tubo de mayor diámetro inyectará más fluido químico por oclusión (atrapa más fluido químico entre dos rodillos pinzados) que un tubo de menor diámetro. Por lo tanto, un tubo grande puede producir más fluido químico con menos oclusiones, lo que resulta en menos desgaste que un tubo más pequeño.
- Diámetro de la cabeza de la bomba – Al igual que el diámetro del tubo, el diámetro del cabezal de la bomba afectará la cantidad de producto químico por oclusión. Los cabezales de bomba de mayor diámetro darán como resultado que se bombee más fluido químico por revolución.
- El número de rodillos – Un modelo de bomba peristáltica determinado puede tener desde uno (rodillo tipo leva desplazada) hasta seis o más rodillos individuales que aprietan el tubo, extraen el fluido capturado y lo envían al extremo de descarga del tubo de la bomba. Múltiples rodillos por conjunto dan como resultado volúmenes ligeramente más pequeños de inyección química por revolución, menos pulsaciones y una probabilidad reducida de que un rodillo individual se desgaste, lo que resulta en una pérdida de capacidad de bombeo. Sin embargo, dado que la vida útil del tubo es directamente proporcional al número de veces que se pellizca el tubo por revolución, el costo asociado con el mayor número de rodillos es la vida útil del tubo.
- RPM del motor: a diferencia de muchos tipos de bombas, las bombas peristálticas son capaces de operar a muy bajas revoluciones por minuto (rpm) mientras mantienen una precisión, repetibilidad y capacidad de cebado muy altas. Por lo tanto, para aumentar la vida útil del tubo, especifique la bomba de modo que su funcionamiento típico se encuentre en el extremo inferior del rango de ajuste de la salida operativa, lo que da como resultado la menor cantidad de oclusiones. Las rpm máximas posibles de un modelo de bomba específico variarán de un fabricante a otro, y las rpm máximas del motor de 650 no son infrecuentes, aunque, a estas altas rpm, la vida útil del tubo se reducirá considerablemente. ¡Algunos modelos de bombas tienen relaciones de reducción efectivas de hasta 10,000 1:0.01, lo que da como resultado unas rpm efectivas mínimas de XNUMX!
- Cantidad de compresión de la tubería – Simplemente apretar (ocluir) el tubo no es suficiente, los rodillos deben apretar el tubo en la cantidad exacta necesaria para garantizar que el fluido que se bombea quede atrapado de manera efectiva en el tubo y se entregue al punto de inyección. Factores como la presión del sistema, la altura de succión, la viscosidad del fluido, el material del tubo y otros afectarán la cantidad de compresión requerida para una aplicación en particular. Si el tubo no está demasiado apretado, el fluido puede escapar o fluir hacia el lado de succión del tubo de la bomba cuando el rodillo gira en el cabezal. Esto puede ocurrir cuando la bomba funciona contra una presión del sistema superior a la recomendada. Si el tubo se aprieta demasiado, estará sujeto a más fuerza de la necesaria y la vida útil del tubo disminuirá. La combinación adecuada del diseño del rodillo con el tipo de tubo que se utiliza dará como resultado el diseño de bomba más eficiente y la vida útil más larga del tubo para una aplicación en particular. La figura 3 muestra la acción de compresión de una bomba peristáltica.
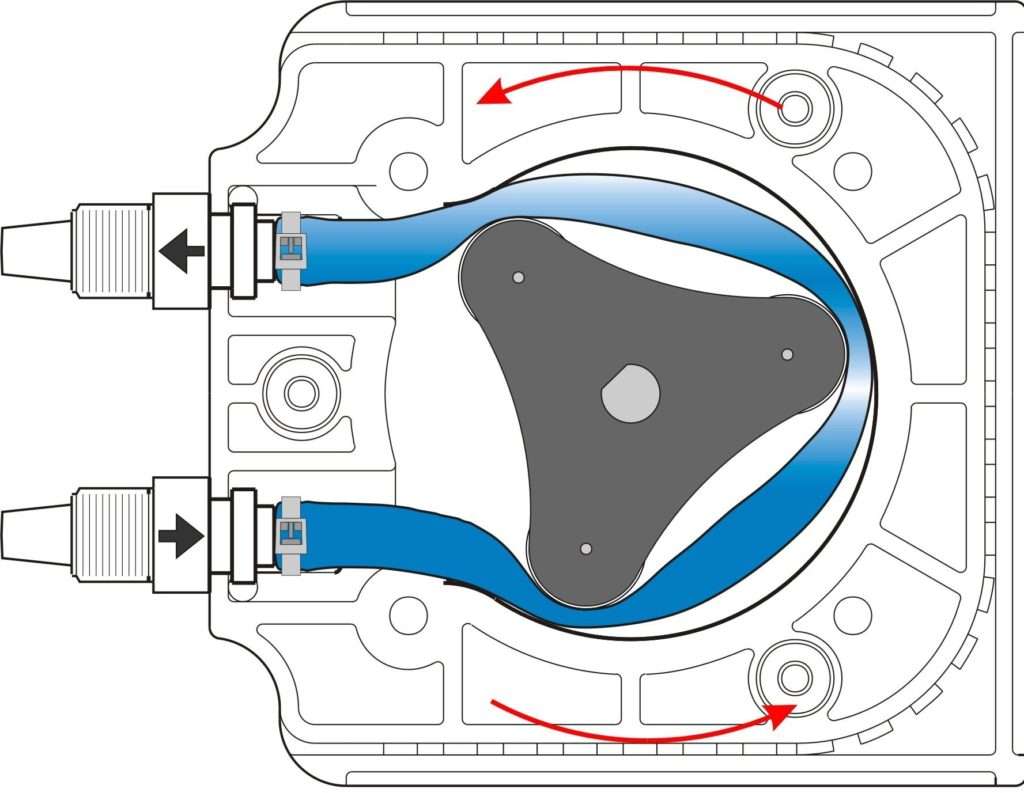
Diseño de cabeza de bomba y rodillo
El diámetro del rodillo, los materiales del rodillo, el tipo de superficies de apoyo y el diseño del cabezal de la bomba también pueden afectar la vida útil del tubo de la bomba, así como la vida útil del conjunto del rodillo. El esquema de un cabezal de bomba se muestra en la Figura 4.
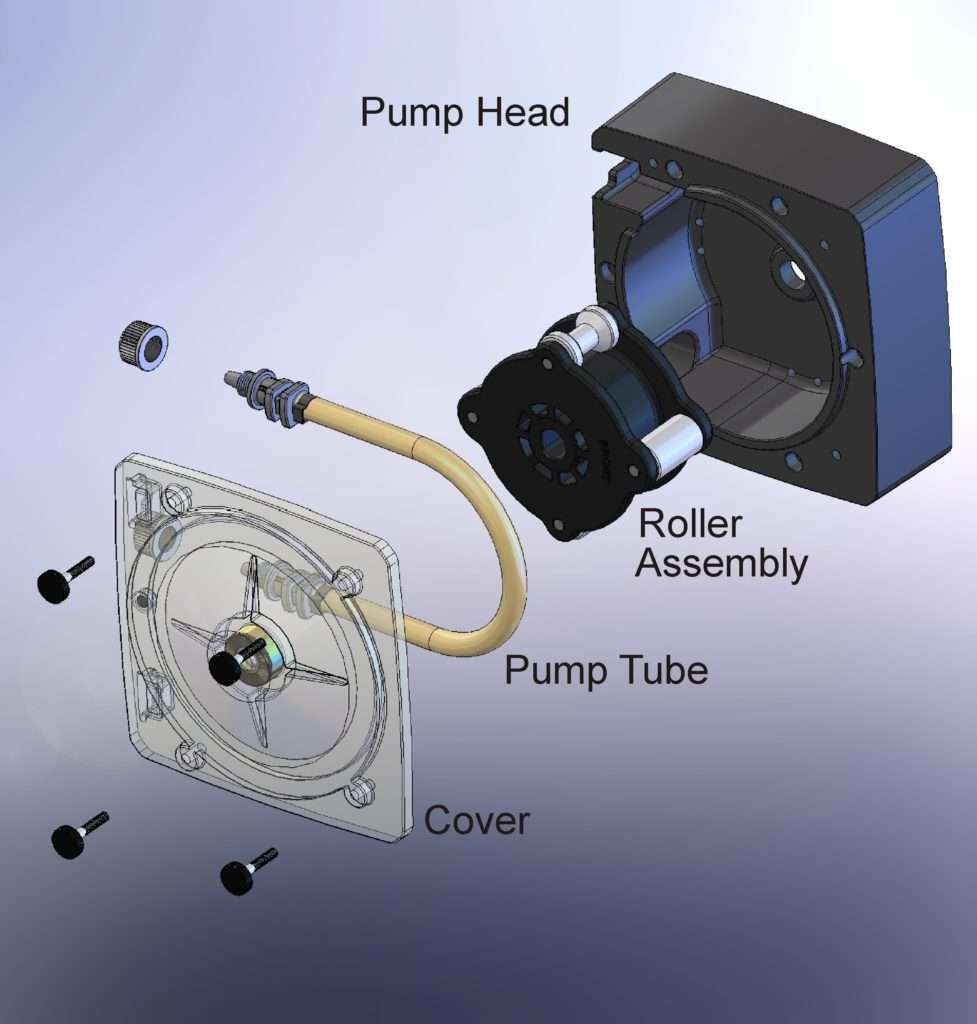
diámetro del rodillo – Un rodillo de gran diámetro aplastará una mayor superficie del tubo mientras gira, lo que reducirá la vida útil del tubo; sin embargo, los rodillos grandes girarán menos revoluciones por revolución del conjunto de rodillos, lo que podría resultar en una vida útil más prolongada.
Rodamientos de rodillos – El rodillo debe girar sobre un eje, por lo que el tipo y diseño de las superficies de apoyo pueden aumentar o disminuir la vida útil del rodillo. El diseño de la superficie de apoyo también puede ayudar a evitar que los productos químicos y los desechos (procedentes del desgaste de la superficie de la tubería) entren en el área del eje del rodillo y causen arrastre en el rodillo.
Material de rodillos – Los materiales de construcción del conjunto de rodillos deben tener la resistencia suficiente para soportar las compresiones repetidas del tubo de la bomba y, al mismo tiempo, ofrecer resistencia a los productos químicos que pueden derramarse en el área del cabezal de la bomba. El conjunto de rodillos también debe tener la estabilidad dimensional para soportar variaciones en la temperatura ambiente y las fuerzas de rotación sin afectar la cantidad de compresión en el tubo de la bomba.
Cabeza de la bomba – Al igual que con el conjunto de rodillos, los materiales de construcción del cabezal de la bomba también deben resistir cualquier derrame de líquido que pueda entrar en el cabezal. El diámetro del cabezal también afectará la cantidad de fluido bombeado por revolución, ya que los cabezales de bomba más grandes descargan más productos químicos por revolución que los cabezales de bomba más pequeños.
Todos los parámetros, como la presión del sistema, el número de oclusiones, la resistencia química del tubo, la compresión del tubo y la ineficiencia del cojinete de rodillos afectan la vida útil del tubo, como se muestra en la Figura 5.
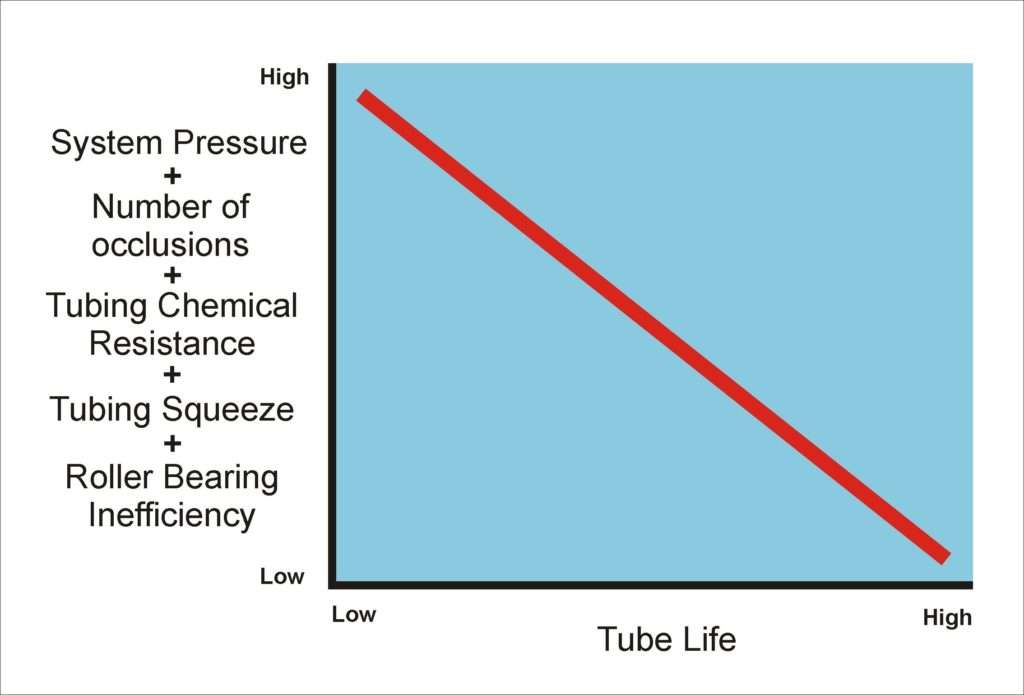
Derrames de sustancias químicas – Si se deja solo, el tubo de la bomba eventualmente fallará. Según la presión de funcionamiento, el tipo de tubo y muchos otros factores, el producto químico puede filtrarse lentamente o salir a chorro de manera espectacular. Los fabricantes ofrecen varios métodos diferentes para proteger el conjunto de rodillos, el cabezal de la bomba y el área que rodea la bomba contra derrames químicos. Algunos fabricantes incluyen puertos de drenaje para eliminar el producto químico, interruptores de flotador para apagar la bomba cuando se produce un derrame y se llena un vaso, y sensores electrónicos para apagar la bomba cuando se detecta el producto químico en el área del cabezal de la bomba. Algunos métodos son más efectivos para apagar rápidamente la bomba y reducir la cantidad de químico derramado. En función de la eficacia del método, el cabezal de la bomba y el conjunto de rodillos pueden sufrir daños que resulten en un arrastre del conjunto de rodillos y una vida útil reducida del rodillo y el tubo.
5.
Motor
Con las bombas peristálticas se utiliza una variedad de motores que van desde pequeños motores de engranajes de CA de polo sombreado de potencia fraccional hasta grandes motores de engranajes de CA y CC con estructura en C. Muchos fabricantes de bombas peristálticas incluyen el motor como parte del conjunto de la bomba, lo que ayuda a eliminar las conjeturas al especificar el motor correcto para usar en un conjunto de bomba determinado. Al igual que con cualquier bomba, se debe tener cuidado para especificar correctamente el motor de la bomba y el entorno operativo previsto.
Electrónica de Control
Los componentes electrónicos de control deben seleccionarse cuidadosamente para controlar correctamente el motor, así como proporcionar cualquier capacidad de comunicación y control remoto, como control de velocidad del motor de entrada analógica, retroalimentación de velocidad de la bomba de salida analógica a SCADA, salidas de alarma, estado de la bomba, etc. motor, muchas bombas incluyen la electrónica de control como parte del conjunto.
Recintos
Por lo general, una carcasa de bomba peristáltica protege el motor y la electrónica de control del entorno operativo, mientras que el área del cabezal de la bomba está desprotegida o sellada en su propia carcasa separada del motor y los controles. Los fabricantes ofrecen una variedad de gabinetes para el motor y los circuitos de control que van desde pequeños gabinetes de plástico hasta gabinetes de metal a prueba de explosiones. Muchas bombas se suministran sin ningún tipo de envolvente. Al igual que con el motor y la electrónica de control, el usuario debe tener cuidado de especificar el sistema de bomba con un gabinete adecuado que esté diseñado para brindar la protección necesaria para el entorno de aplicación, como se muestra en la Figura 6.
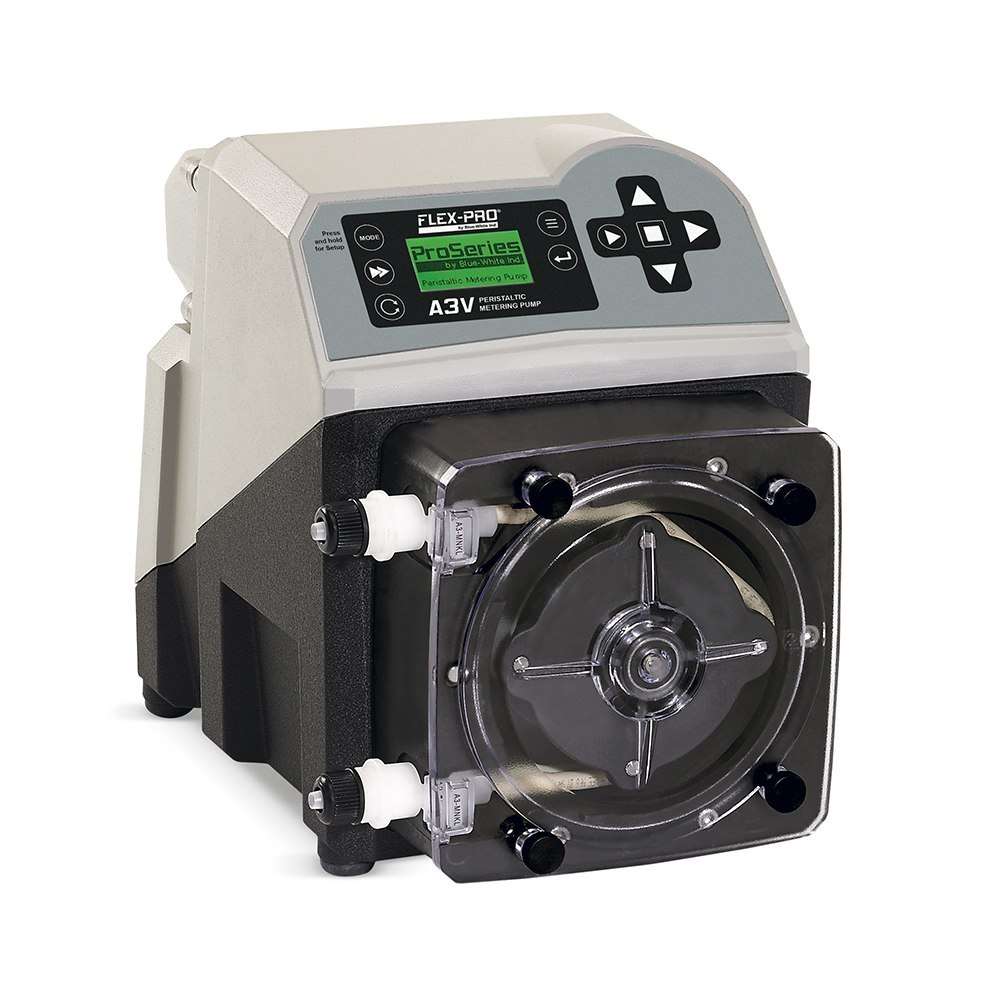
En la Figura 7 se muestra una configuración típica de bombas peristálticas con un motor y un controlador integrados que proporcionan la alimentación química necesaria al sistema de agua de refrigeración.
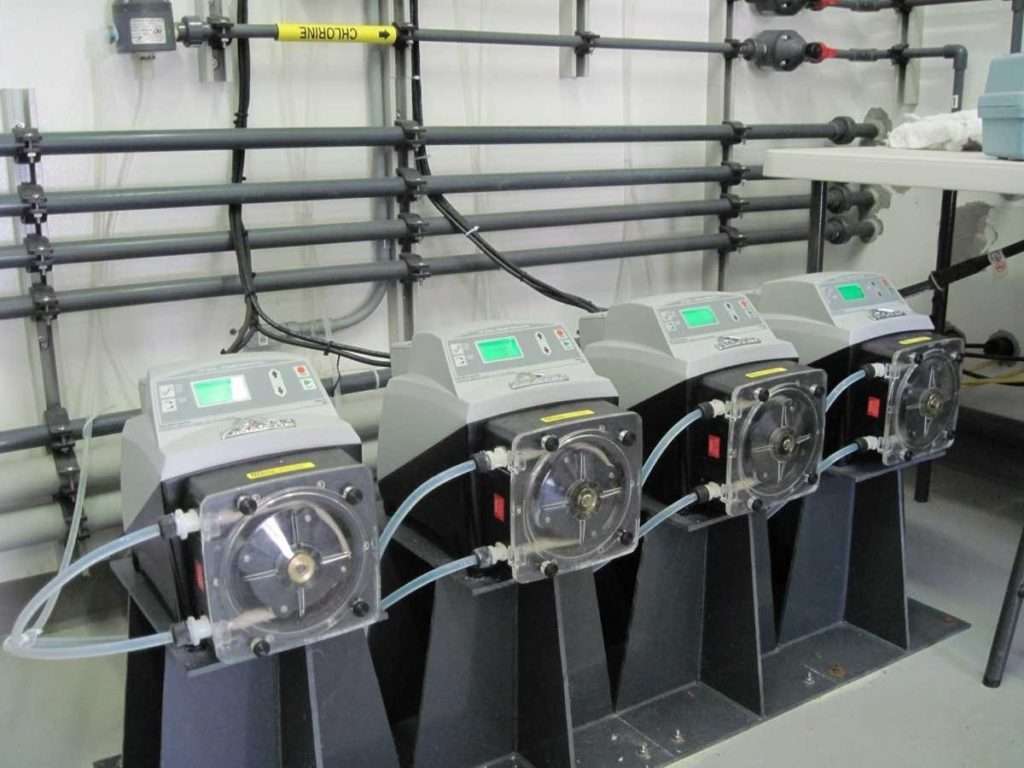
Conclusión
Muchas variables afectan la vida útil y los requisitos de mantenimiento de una bomba peristáltica. Al evaluar cuidadosamente la aplicación, el usuario puede especificar correctamente la bomba y los componentes para minimizar los requisitos de servicio y mantenimiento y maximizar la vida útil de la bomba.
El Sr. Bill McDowell es ingeniero de ventas con Blue-White Industries y tiene más de 29 años en la empresa. Ha ocupado diversos cargos con Blue-White Industrias que incluyen ingeniero de proyectos y director de ingeniería. Se puede obtener información adicional de Blue-White Industries en, 5300 Business Drive, Huntington Beach, CA 92649. Teléfono 714-893-8529, Fax 714-894-9492, o ventas @blue-white.com; www.blue-white.com